Capabilities and Services
Capabilities
Box Build, PCBA, Cable Harness, and Testing
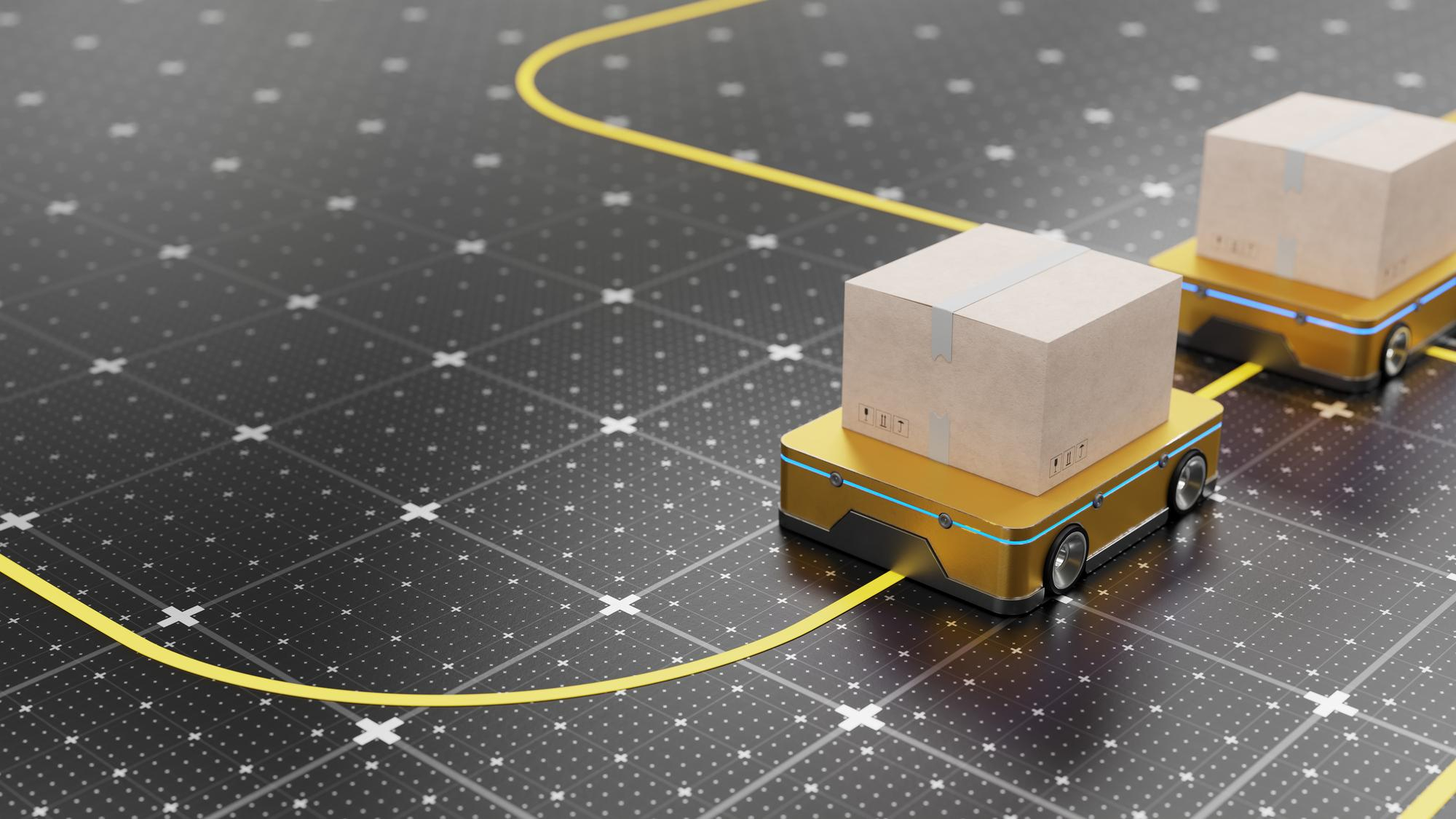
Procurement and Materials Management
a. Purchasing and supply chain
b. Receiving and incoming inspection
c. Kitting
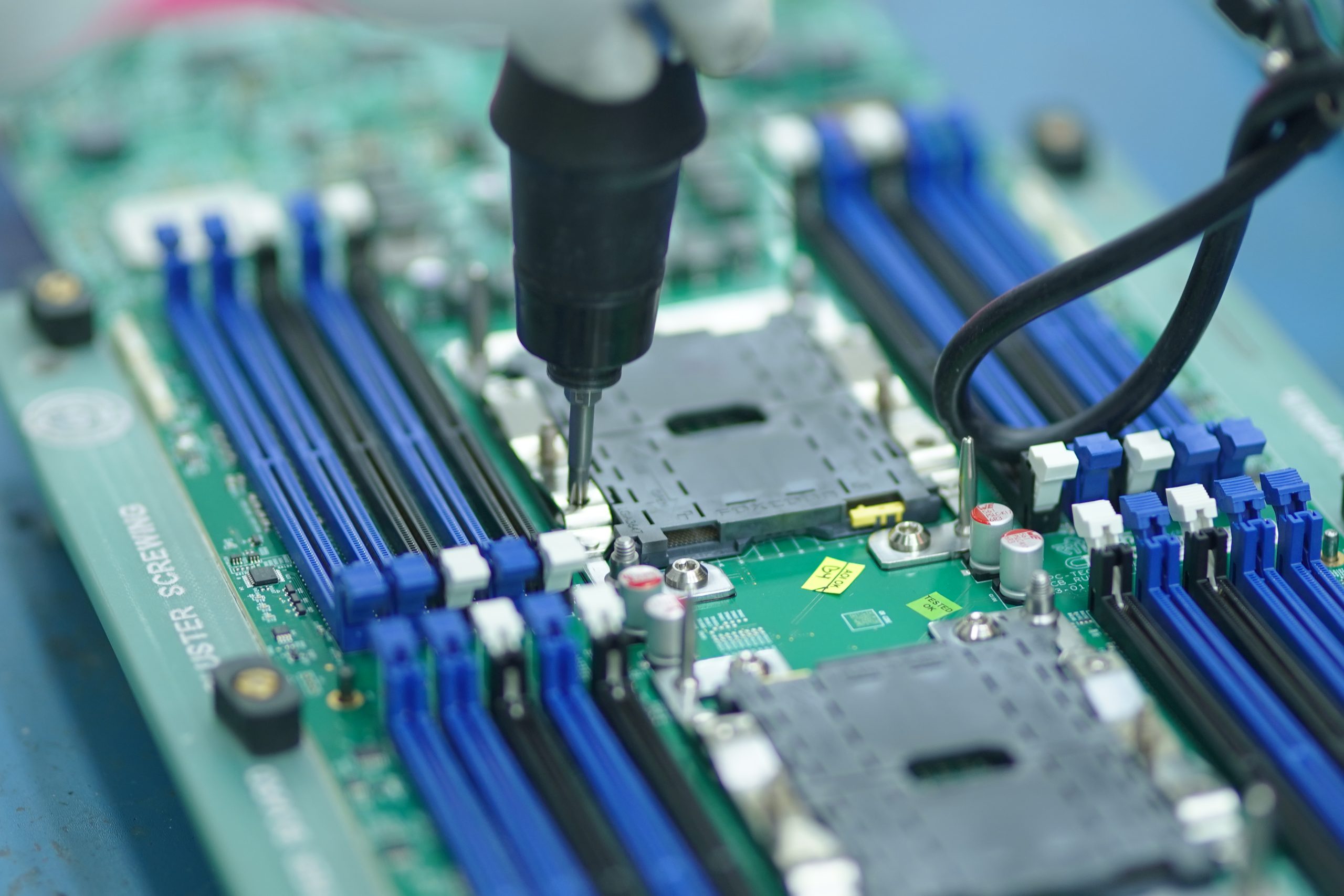
Manual and Automated Soldering Expertise
a. Solder paste printing
b. Selective soldering
c. Component placement
d. Manual assembly
e. Solder reflow
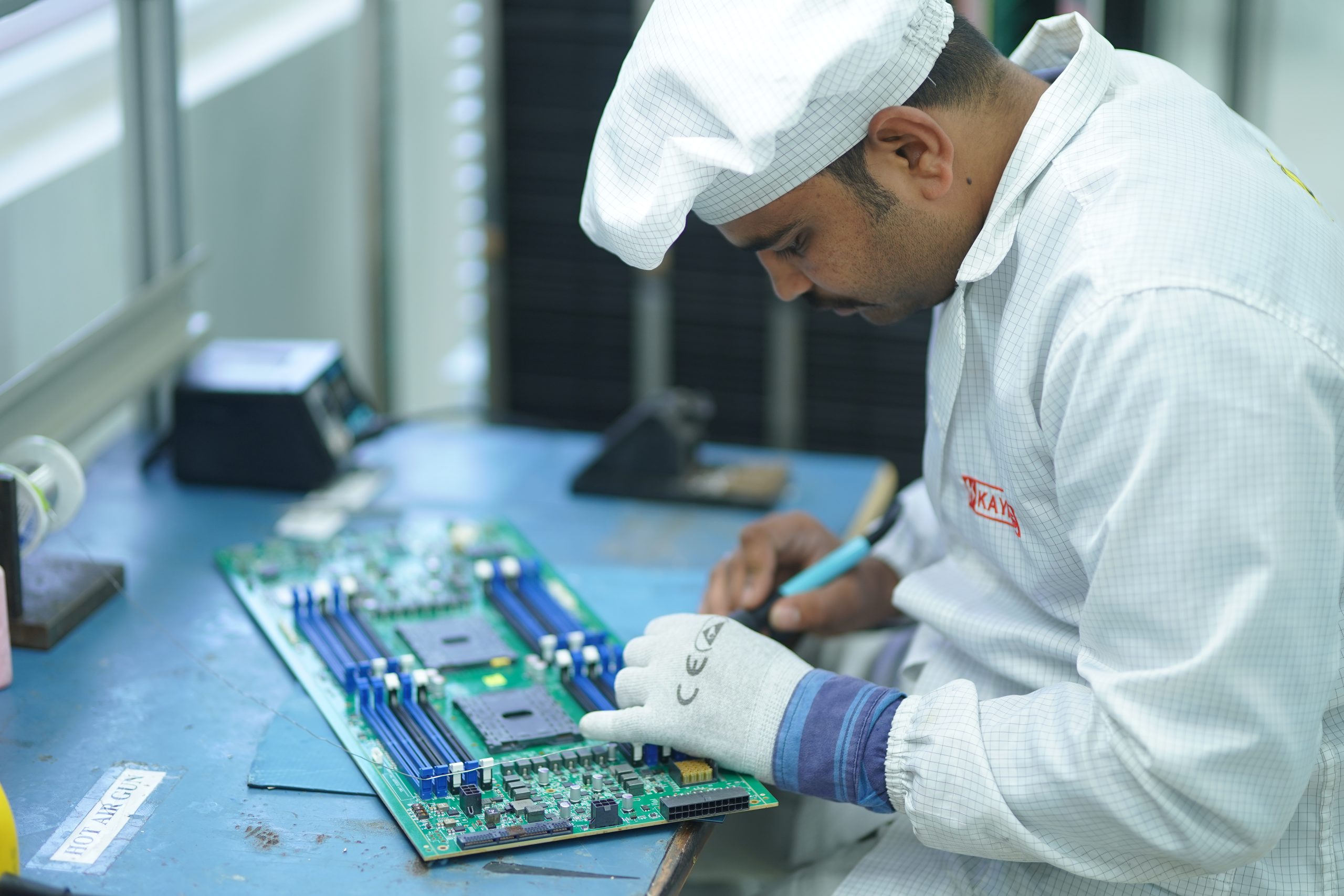
End-To-End Testing Solutions
a. Burn-In testing
b. Functional testing
c. Optical and X-Ray inspection
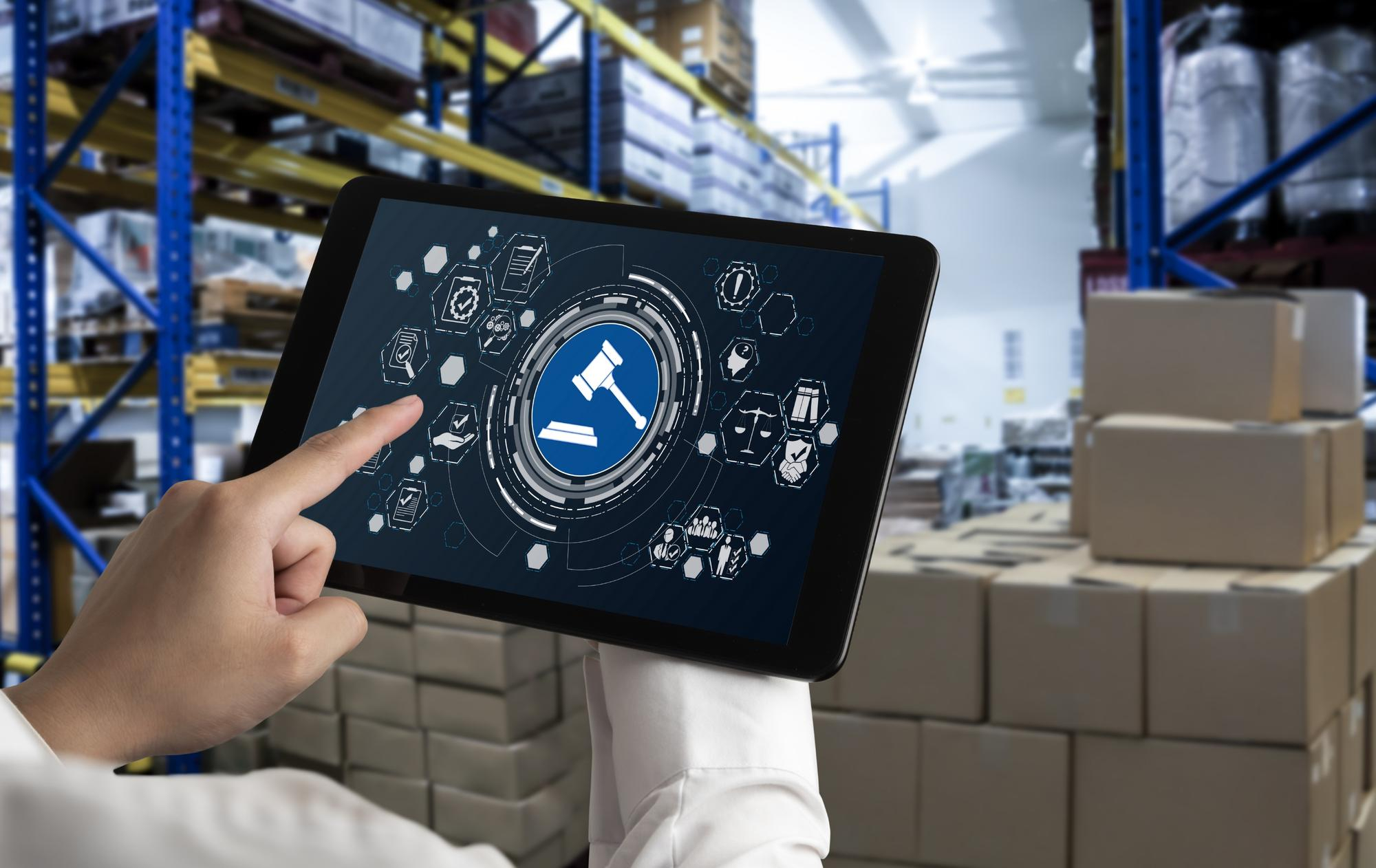
Quality Assurance and Entire Product Fulfillment
a. Cleaning
b. Final inspection & QA
c. Final assembly/ Labelling
d. Packaging and shipping

Turnkey Manufacturing Consignment Manufacturing With Program Management
Purchasing & Supply Chain
Component integrity and quality are keys to long term reliability of board assemblies.
Digicom has extensive experience with sourcing hard-to-find and specialty electronic components. At Digicom we only buy from franchised sources, unless specifically directed by the customer. Customers have full visibility of sources and prices across the Bill of Materials. Where appropriate, we will suggest potential areas to save cost or board real estate and these savings are passed directly to you, our customer.
Receiving and Incoming Inspection
Advanced and detailed labeling give even greater traceability to the process.
Every reel or tray of components is 100% visually inspected at receiving and labeled for accurate tracking, moisture sensitivity, and shelf life expectancy.
Receiving and incoming inspection is a crucial step in the manufacturing process, as it ensures that all materials and components used in production meet the required quality standards. This process involves carefully inspecting and documenting all incoming materials, components, and products, to ensure that they meet the specifications outlined in the order.
By using barcodes, RFID tags, or other forms of identification, it is possible to quickly and easily track the origin and history of each item, making it easier to identify and correct any issues that may arise.
Quality is an essential aspect of receiving and incoming inspection, as it directly impacts our ability to meet ISO qualifications and customer satisfaction. By implementing rigorous inspection protocols and documenting all findings, we can ensure that we are providing high-quality products to our customers, which in turn leads to increased satisfaction and repeat business.
ISO qualifications are an important measure of a company’s commitment to quality, and receiving and incoming inspection plays a key role in achieving these qualifications. Through the use of detailed documentation and the use of advanced inspection techniques, we can demonstrate that we are adhering to the strict standards required.
In addition to ensuring compliance with ISO qualifications, receiving and incoming inspection is also crucial for maintaining customer satisfaction. By providing high-quality products and materials, we can ensure our customers are satisfied with our products, leading to increased loyalty and repeat business. That’s why we have a robust and well-defined process of incoming inspection in place to meet the high expectations of our customers.
Kitting
Attention to these details is vital to obtaining the maximum performance from the SMT line.
Kitting is an essential part of the preparation in an efficient EMS assembly house to make sure the correct number of components are used, so the assembly line is not slowed down or stopped, and to check to see that parts are within their “use by” date and their position is optimized on the feeder bank. Attention to these details is vital to obtaining the maximum performance from the SMT line.
Digicom’s newly expanded stock room is fully organized and stocked, inventory is maintained, and there’s plenty of room to spare.
Solder Paste Printing
Solder paste not only performs the function of a physical interconnection material, but it is the structural support, thermal interface and conductor.
It is critical to the manufacturing process that the correct amount of solder is applied in exactly the right place.
Digicom has the latest in solder stencil printing equipment. We can accommodate a wide range of print formats. A laser-guided printer uses a scanning camera to quickly locate the fiducials and align the tooling and the PCBs accurately, while the transport system processes the boards with a minimum of handling time and the solder paste height detection system guarantees the correct height of the fillet. The easy-to-use touch screen makes programming faster and more precise.
The printer prints and inspects each pad and solder joint after the solder is applied, ensuring the accuracy and reliability of the printing. PCBs are inspected thoroughly for excess paste, missing paste, bridges, and other defects or anomalies.
Lead-free and tin-lead soldering options are available. Leaded components are processed through our state-of-the-art wave soldering system. For larger production runs we use a laser guided printer that uses a scanning camera to quickly locate the fiducials and align the tooling and the PCBs accurately.
Component Placement
Digicom can handle the most challenging component packages that exist today.
Flexibility, fast change-over, quick set-up, outstanding accuracy, and excellent repeatability define Digicom’s pick and place process. Placement systems at Digicom are able to handle a wide array of board sizes, the smallest components, and complex boards. Programs, configuration, and feeder systems are inspected and verified before each operation.
First articles are inspected and verified before each production run. Full traceability is provided. Whether it’s high volume low mix or high mix low volume, Digicom’s new pick and place equipment can handle the most challenging component packages that exist today.
Solder Reflow
Digicom's use of precision profiling results in the highest quality during the soldering process, since the temperature is controlled precisely at each zone.
Digicom’s advanced high-throughput convection reflow oven generates customized time-temperature profiles for each board. A gold super-mold module attached to the PCB travels through the reflow oven gathering data on thermal characteristics. Sensors are strategically attached to the PCB to record data at a maximum rate of 5,500 points per second and then transfers the data to the on-board computer. Complex algorithms and associated software take into account the sensor readings, solder paste characteristics, and other variables pertinent to each particular assembly. A target profile is generated and set-points transferred to the oven configuration.
Digicom’s convection oven optimizes both lead-free and leaded processing, even for high density boards, for the ultimate in productivity and efficiency. Closed-loop convection control provides precise heating and cooling, programmable heat transfer, and reduced nitrogen consumption.
Long multiple heating and cooling zones allow smooth, precise profiling with high speed controlled zone-to-zone transitions and an exit temperature below 80°C. Incredibly powerful analytical capabilities and excellent profile control enable Digicom to ensure an exacting reflow process that results in the highest quality.
Selective Soldering
Speed, accuracy, high yield, and superior throughput are some of the benefits of Digicom's selective soldering process.
Before selective soldering begins the board is fluxed and preheated. A personalized time/temperature profile is calculated and true top-side preheat maintains the temperature of the board throughout the process.
Through-hole components are soldered efficiently with repeatable high-quality solder joints. Digicom’s selective soldering system can solder any site, any orientation, anywhere on the board.
Cleaning
Digicom's Diamond Track Cleaning Process is what sets us apart from our competitors.
With increased component miniaturization, electromigration and the rising cost of advanced packages, it is essential to thoroughly clean today’s high reliability electronics.
Digicom’s process uses a unique customized, in-line cleaning system that repeatedly delivers zero ion contamination as measured and backed by independent certified lab reports.
Independent tests show that Digicom’s Diamond Track process results in boards that are 75% cleaner than the IPC’s* highest level of clean. A recent lab analysis for ion contamination found zero ion contamination (zero levels of sodium chloride–NaCl Micrograms/sq.in.) on assembled boards. The process is completely “green”. Deionized water from polishing tanks is used and recycled. Filters catch the solids while powerful blowers ensure that harsh chemicals are not blown back into the tank. Clear windows enable the operator to monitor the entire process. A refractometer checks the stability of the tank to make sure it’s not compromised. All drained solids are environmentally friendly.
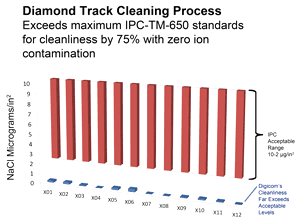

The cleaning process is repeatable, reliable, and uses an advanced in-line cleaning system to increase speed and throughput. All boards are routinely run through the system prior to assembly to ensure that the soldering process is not compromised by any contaminates from board fabrication and after assembly to completely clean any remaining chemicals from the soldering process. With Digicom’s unique Diamond Track Cleaning the customers’ products are much less susceptible to corrosion-induced failures reducing the need for maintenance or repair.
The cost savings to Digicom’s customers, especially those with military, aerospace and medical device applications, is considerable. The Diamond Track process eliminates failures from contamination that often result in millions of dollars in rework and repair, recalls, lawsuits, and lost business and revenue, and it protects the company’s brand and reputation.
* IPC Association is a global trade organization and leading source for industry standards, training, market research and public policy advocacy. Ref: IPC-TM-650 Standard for Cleanliness.
Optical & X-Ray Inspection
Our automated optical inspection (AOI) is complemented by an x-ray system for an even closer look at BGA bumps and other hard to reach areas.
At Digicom we take inspection very seriously to ensure that no defective boards leave our factory. Inspections are done at every station along the manufacturing process and every board is tested.
Our latest Automated Optical Inspection machine is lightning fast and is armed with 15 megapixel cameras. Using laser triangulation, each board can be accurately inspected for lifted leads, planarity of BGA devices and other packages, and many other defects.
Manual Assembly | Soldering | Fastening
Nothing beats the experienced eye of a production engineer who is familiar with every step of the board's design, prototyping, fabrication, and first article runs.
Despite all our automated systems and equipment, Digicom still employs manual inspection at every part of the process. Nothing beats the experienced eye of a production engineer who is familiar with every step of the board’s design, prototyping, fabrication, and first article runs.
Solder deposits are examined and touched-up where needed and components, their orientation, and connections are checked.
Functional Test
During functional test, each step of the assembly process is carefully recorded electronically and inspection points and sequences are set.
Each operator has a unique ID that allows full traceability of the tests that were performed, when, and by whom. These test stages combine to form our Production Control Traveler.
Final Assembly | Labeling
Besides board assembly, Digicom's expertise includes mechanical assembly and final box build.
Digicom supports a wide array of mechanical modules for your design, both metal and plastic. These range from simple, off-the-shelf enclosures to large, customized cabinets and racks. We also support bare boards when the customer handles the enclosures at the final assembly location.
Before any enclosures are fastened, the required torque is checked. Every part used is documented and tracked. Advanced and detailed labeling give even greater traceability to the process.
Burn-In
Burn-in test involves multiple ramp-ups to maximum temperatures and extreme conditions where dry solder joints or weak components will be exposed.
At Digicom we use burn-in test to stress test the finished board assemblies to detect any signs of likely failures before the board is mounted into the final assembly or released to the client.
Final Inspection and Quality Assurance
Before your product leaves our factory it is subjected to a rigorous final inspection. We delight in offering a first pass yield of over 98%.
This is achieved through our meticulous attention to detail, our use of only the best components and materials, and the many years of experience of the Digicom team. Many of Digicom’s employees have worked at Digicom for 10-20 years.
At Digicom, we understand that final inspection and quality assurance are crucial steps in the manufacturing process. That’s why before any product leaves our factory, it is subjected to a rigorous final inspection to ensure that it meets the required quality standards. Our team of experienced inspectors use advanced equipment and techniques to thoroughly examine each product, checking for defects, inconsistencies, or other issues.
We are proud to offer a first pass yield of over 98%. This means that 98% of the products we produce pass our final inspection on the first attempt, ensuring that only the highest quality products are shipped to our customers. This level of quality control is achieved through a combination of careful planning, strict protocols, and the use of advanced inspection equipment.
At Digicom, we understand that customer satisfaction is the ultimate goal of our quality assurance process. We go above and beyond to ensure that our products meet the highest quality standards, so that our customers can be confident that they are receiving products that they can rely on. By providing high-quality products and excellent customer service, we strive to build long-lasting relationships with our customers.